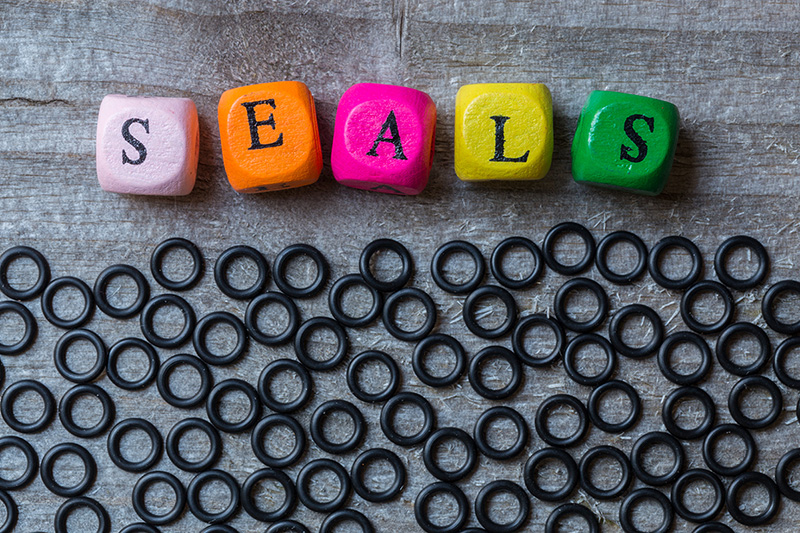
Selecting the right type of O-Ring for a specific application involves careful consideration of several key factors to ensure optimal performance, longevity, and reliability. Here are the essential factors to keep in mind:
-
Material Compatibility: The compatibility of the O-Ring material with the fluids, chemicals, and gases it will come into contact with is crucial. Different materials have varying resistance to specific substances. Ensure the chosen material won't degrade or swell when exposed to the application environment.
-
Temperature Range: Consider the temperature extremes of your application. Some O-Ring materials perform better at high temperatures, while others excel in low-temperature environments. Choose an O-Ring material that can maintain its integrity within the intended temperature range.
-
Pressure Resistance: Evaluate the pressure levels your O-Ring will experience. Different materials and designs can handle varying levels of pressure. Ensure the O-Ring is rated for the maximum pressure it will encounter to prevent leakage or failure.
-
Application Type: Determine whether the O-Ring will be used in dynamic (moving) or static (stationary) applications. Different materials and designs are suitable for each type, as dynamic applications require materials with better wear resistance and flexibility.
-
Size and Dimensions: Accurately measure the groove dimensions and cross-section of the O-Ring cavity to ensure a proper fit. Choosing the correct size prevents leakage and ensures effective sealing.
-
Industry Standards and Certifications: Consider relevant industry standards, certifications, and regulations that may apply to your application. Adhering to these standards ensures compliance, safety, and reliability.
-
Environmental Factors: Assess any environmental factors, such as exposure to UV radiation, ozone, or weathering. Some materials are better suited to withstand outdoor conditions, while others may degrade over time.
-
Fluid Type: Understand the type of fluid (liquid or gas) that the O-Ring will seal. Different fluids can affect the material's compatibility, swelling, and performance.
-
Friction and Wear: In dynamic applications, friction and wear are important considerations. Choose a material that offers low friction and wear resistance to prevent premature failure.
-
Assembly and Installation: Consider the ease of installation and assembly. Some O-Ring materials may be more challenging to install, requiring lubrication or specific installation techniques.
-
Longevity and Maintenance: Determine the desired service life of the O-Ring. Some materials and designs offer longer lifespans and reduced maintenance intervals, which can be crucial in critical applications.
-
Cost-effectiveness: Balance performance requirements with budget constraints. While premium materials may offer superior performance, they might not always be necessary for every application.
-
Specialized Requirements: If your application has unique demands, such as high purity, medical compliance, or resistance to aggressive chemicals, look for specialized O-Ring materials that meet these requirements.
-
Consultation: When in doubt, consult with O-Ring manufacturers, suppliers, or engineers. Their expertise can help you navigate the available options and choose the best O-Ring for your specific application.
By carefully considering these factors, you can make an informed decision and select an O-Ring that will effectively seal and perform within your application's unique conditions.
Need help selecting the right O-Ring?
Our experts have crafted several helpful resources to explore:
- Learn about the various O-Ring types and materials in our guide Seal the Deal: Your Guide to O-Rings.
- Learn about product performance standards in O-Ring Industry Standards and Certifications.
When it comes to O-Rings, we’re trusted experts. Contact us or call 800-669-9650 to speak with a member of our customer service team at any of our 11 locations (Knoxville, TN; Marietta, GA; Orlando, FL; Charlotte, NC; Little Rock, AR; Fort Worth, TX; Benton, IL; Madisonville, KY; Princeton, WV; Birmingham, AL; Calvert City, KY).